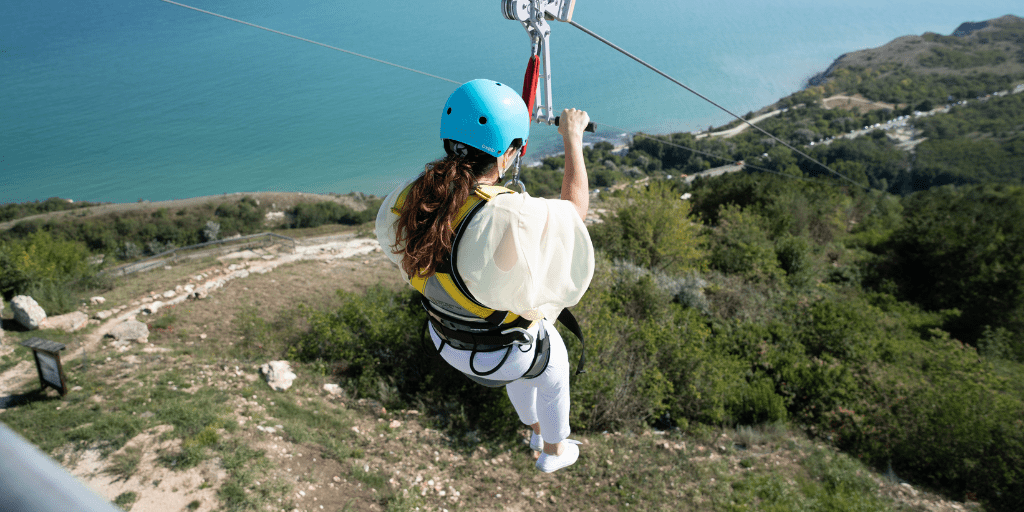
Operators should have faith in their braking systems while being aware that unforeseen problems with the primary brake could arise from things like flaws in third-party equipment and mistakes made during setup, upkeep, or operation. According to ACCT and ASTM standards, every zip line installation with an arrival speed more than 10 kph (6 mph) must have an emergency arrest device (EAD).
When stopping a participant at a zip line’s end, speeds greater than 10 kph (6 mph) cause dynamic effects on the human body. Understanding the forces that may be applied to the body as it stops moving safely is important, as is having a well-designed braking system and a suitable emergency brake (EAD).
The definition of a zipline brake system
A zipline brake system is a combination of primary and emergency brakes intended to stop a person’s motion. An emergency brake is a brake installed on a zip line that engages without participant input when the primary brake fails to stop the zip line in order to prevent serious injury or death.
Guidelines for ziplines and their braking systems are established by the American Society for Testing and Materials (ASTM) and the Association for Challenge Course Technology (ACCT). The Emergency Arrest Device (EAD), often known as an emergency brake, is required by ACCT regulations under certain conditions. Zipline braking systems must comply with ASTM criteria and be fail-safe.
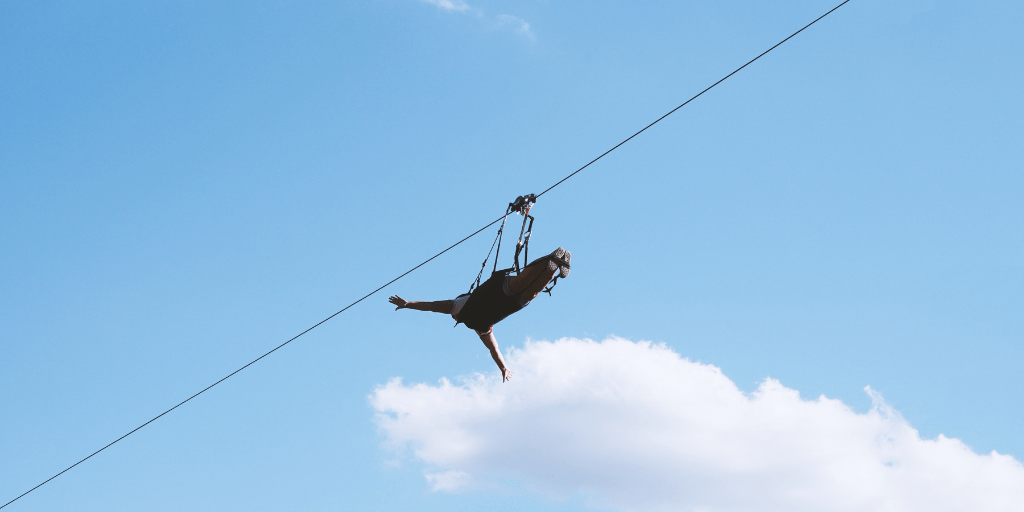
ACCT Standards and Definitions:
- Brake System: A system of primary and emergency brakes designed to stop a person’s mobility simultaneously.
- Emergency Brake: A zipline brake that, in the event that the primary brake fails, engages immediately and without participant input, averting serious damage or death.
A zipline braking system must address “the level of risk posed to the participant by the brake system’s failure or any of its components, including potential for pinching, binding, entanglement, etc.” according to ACCT guidelines. A “qualified person” should also evaluate “brake system operational characteristics at the extremes of the design continuum for participant weight and arrival speed.”
ASTM Standards and Definitions
*Note: The relevant sections of ASTM F2291 and F2959 are included in the following standards.
- Braking System: When discussing aerial adventure courses, braking systems may include, but are not limited to, longitudinal friction brakes, disc or drum brakes, and motor end brakes, either onboard or off-board of the patron-carrying vehicle or gadget. The brake system must be fail-safe if a malfunction leads to a dangerous situation.
- Fail-Safe: A feature of an aerial adventure course or its parts that is intended to guarantee that typical and anticipated failure modes result in a safe situation.
According to ASTM standards, “the designer/engineer shall perform and document an analysis of the ride demonstrating how hazards to persons have been managed.” The failure analysis in this report must take the form of “a Fault Tree Analysis, a Failure Mode and Effects Analysis (FMEA), or other accepted engineering practice.”
Why it Is Not Recommended to Use Guide-Operated Emergency Brakes:
A standard zip line will feature a primary brake that can effectively stop any rider on the line in a safe location. No matter what kind of primary brake is used, a sufficient EAD is necessary to guard against unanticipated failures of the primary brake. What would stop a person at the end of a zip line, for instance, if they were to pass out while using hand braking as the primary brake? To stop all riders safely, a backup mechanism needs to be in place.
Zip line guides are more likely to suffer major injuries than users, according to anecdotal evidence. The main factor is that they experience zip lines more frequently than the average participant, considerably increasing their exposure. The likelihood that something may finally occur increases the longer you engage in a risky activity. The most probable person to experience a primary brake malfunction is the one who rides the zip lines the most frequently, according to statistics. Guides should be given the same safeguards as the paying consumer in order to protect them. Therefore, it is not advised to use guide-activated emergency brakes as EADs.
The Effects of Gravitation Persisted Despite Deceleration
During terminal deceleration, there is a chance of serious injury or death due to a number of factors. The participant’s object of halt, their alignment, the tools used, and other elements may all be factors. G-load, often known as the weight-like sensation brought on by deceleration, is a helpful statistic for understanding the forces a rider encounters during braking. An individual experiences 1 G vertically (their body weight) while standing on Earth. When a driver uses the brakes firmly, significant horizontal g-Loads result, but light braking results in negligible g-loads. More significant g-loads are experienced by objects slowing over shorter distances than by those slowing over longer ones.
A participant will actually feel the least and greatest g-loads. As the springs compress, a spring pack will provide increasing deceleration, leading to higher g-loads than those calculated in the example. Additionally, because a participant is not rigidly attached to a trolley, they are free to swing, which may increase the braking distance and reduce g-loads. Theoretical data can serve as a base, but a wide range of variables affect emergency braking scenarios. Therefore, the preferred method for verifying an EAD is real-world testing with purpose-specific test equipment carried out by an experienced designer or engineer. Such testing is defined by ASTM F2137 Standard Practice for Measuring the Dynamic Characteristics of Amusement Rides and Devices.
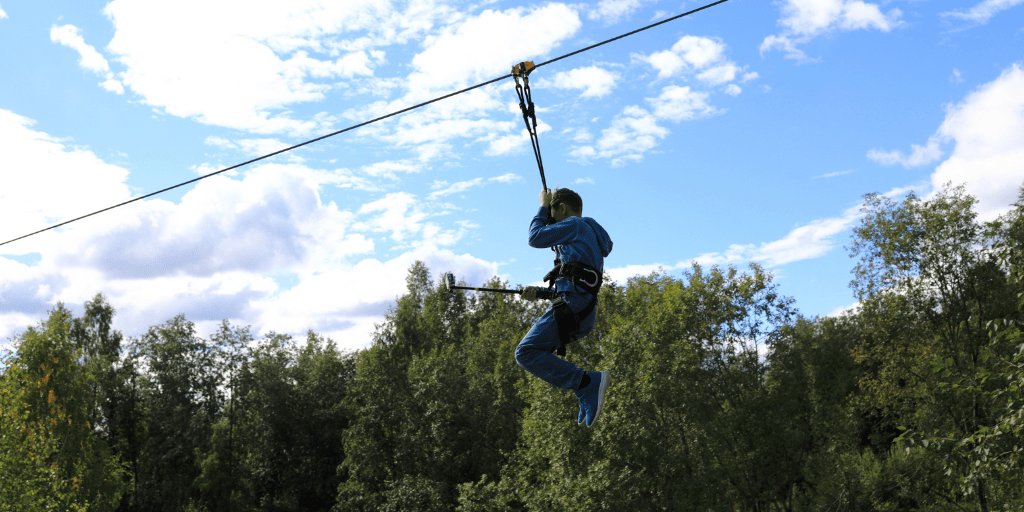
Test requirements for a zip line brake system
According to the ACCT rules, an emergency brake is a zip line brake that engages on its own when the primary brake fails, preventing catastrophic damage or death. We do not recommend any particular brands or gadgets, and neither do the standards. Installers, operators, and builders must make sure that the zipSTOP Zip Line Brake is installed and used in accordance with ACCT and/or ASTM standards, the Operators Manual, and the appropriate EAD because each zip line installation is unique.
A qualified person must develop the procedures, oversee the execution, and assess the results of operational tests. All assessments should show the following:
- Operational parameters of the brake system for participant weight and arrival speed at the extremes of the design continuity
- Verification of the brake system’s dependability and intended performance
Since an emergency brake is a component of a complete brake system, as described by ACCT, it must be tested in accordance with ACCT standards if both of the following take place after the primary brake fails:
- The person travels faster than 6 mph (10 kph) to the zip line landing place.
- The participant comes into touch with persons, objects, or the ground in the zip line landing area without their consent or in a damaging way.
Performance Testing must be done, according to ASTM F1193:
- Performance testing should include a number of prescribed tests that can be performed to assess whether a newly constructed ride or gadget complies with the original design requirements.
The brake system must be tested to determine that it is in fact fail-safe because the original design criteria required that it be fail-safe. We Technologies advises detaching the primary brake and sending a variety of test weights (unmanned) down the zip line to assess the efficacy of a suggested EAD. Watch how the weights and arrival speed will affect the suggested EAD. It is not an emergency arrest device if it could cause serious harm or death or if the outcome is unsafe.
Even though it isn’t stated explicitly in the ASTM or ACCT standards, it is important to remember that specific circumstances can have a big impact on a participant’s arrival speed. Strong winds, wet weather, and cold temperatures can all significantly increase rider arrival speeds; these factors should be taken into consideration by the primary brake and EAD during testing.
To sum up
A comprehensive zip line brake system must have both a main brake and an EAD because they are both vital to risk mitigation. The primary brake and EAD on your zip line should be carefully designed, fitted, and tested since in some dire situations, they could mean the difference between life and death. This is why, in accordance with ACCT and ASTM requirements, we require the use of EADs in all zip line installations using the zipSTOP Zip Line Brakes.
The entire zip line industry is intended to gain from these standards and our EAD criteria. The confidence in the sector will increase as a result of lowering risk, boosting dependability, and reducing accident incidents, which will promote industry health as zip lining becomes more popular. We propose performing physical tests and regular inspections to ensure the efficiency of all braking systems and making sure your primary brake and EAD are built to withstand worst-case scenarios.
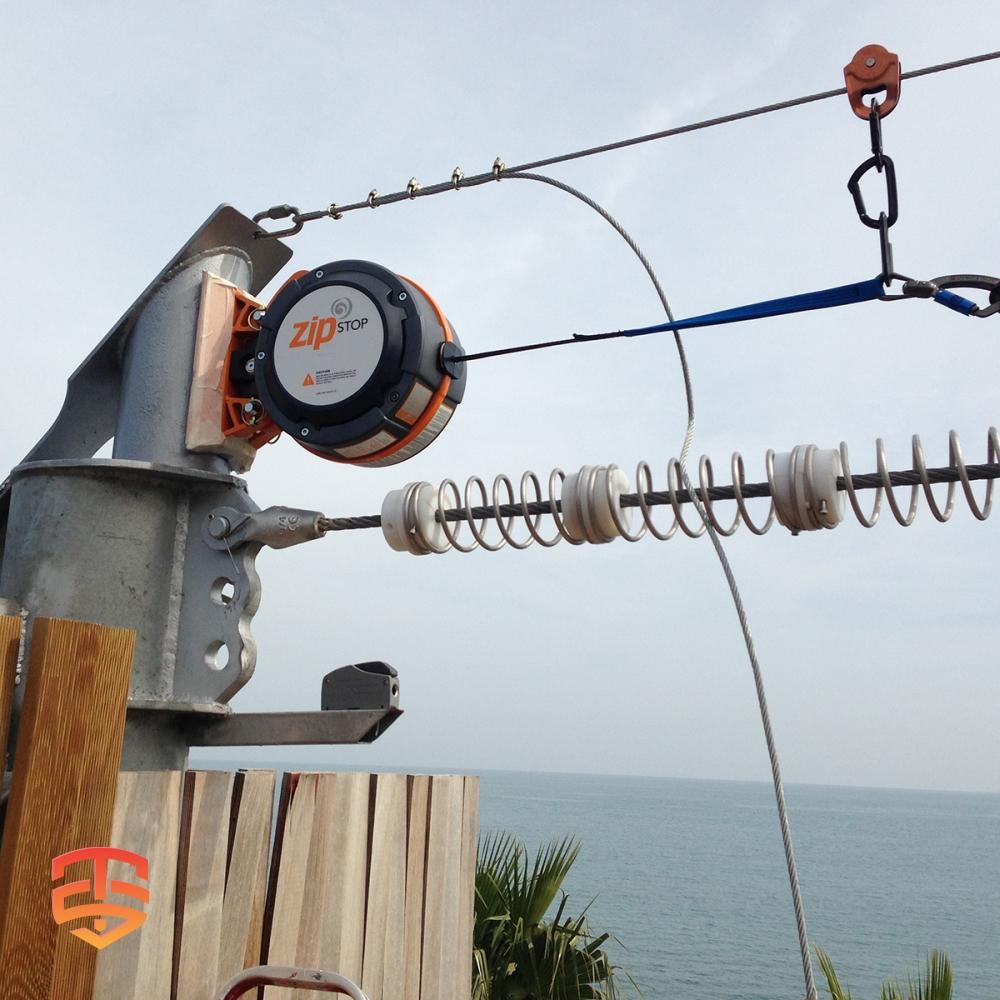
Zipline Safety Solutions
We deliver a complete professional Zipline system, from our Self-braking Magnetic Zipline Trolley to a safe Zipline Spring Brake.
We offer a full family of zip line brakes that increase throughput with a hands-free braking experience for zip line riders and operators, and a full ecosystem of zip line products to outfit the best zip line builds in the world. We use advanced technology to engineer and manufacture innovative adventure equipment for the outdoor, amusement and recreation industries.
Beyond the Basics: Unveiling Zipline Technology with Expert Analysis
Intrigued by the potential of Zipline technology? You’ve come to the right place! This article provides a solid foundation. But if you’re eager to delve deeper and gain insights from industry experts, keep reading…
- Zip Line Design: Components for a Complete System
- Considering operating and investing in a zipline?
- 9 Zipline Mistakes You Don’t Know You’re Making
- Magnetic Zipline Braking: A Revolutionary Way to Ensure Safe Rides
- Pros and Cons of Different Zip Line Brakes
- Expert Tips for Zip Line Brake Installations
- White Paper on Zipline Emergency Arrest Devices (EAD)
- The Importance of Optimizing Zip Line Design for Rider Speed
- Does your zip line need an emergency arrest device?
- The Magnetic Self-braking Zipline pulley
- Zipline Braking and landing considerations
- Why Zip Line Trolley Bearings Matter
- Whitepaper: Zipline Braking Dynamics
- Zip Line Installation: Give them the Best Ride
- How to startup a Successful Zip Line Business
-
zipSTOP IR Zipline Brake | 24 – 60 kph€ 5.649,00 – € 5.799,00 Ex VAT
-
zipSTOP SPEED Zipline Brake | 50 – 72 kph€ 6.099,00 – € 6.349,00 Ex VAT
-
Spring Brake System | Primary & EAD zipline brake€ 80,00 Ex VAT